Comprehensive Guide to Effective Packaging Maker Repair Strategies for Ideal Performance
Efficient product packaging device repair is critical for maintaining functional continuity and product top quality in today's fast-paced production setting. Understanding usual issues, such as imbalance and digital faults, is only the start. Employing an organized approach to diagnostics and repair service, alongside precautionary upkeep methods, can considerably improve equipment longevity and efficiency. Nonetheless, the nuances of applying these strategies properly might not be instantly apparent, prompting further expedition into the certain approaches and tools that can transform a professional's strategy to upkeep. What fundamental methods could redefine your upkeep strategy?
Typical Packaging Machine Issues
Product packaging makers, crucial for reliable production lines, frequently come across a number of typical problems that can interrupt procedures. One common problem is imbalance, which can cause improper sealing or classifying, eventually impacting item stability and presentation. This imbalance might come from damaged parts or improper arrangement throughout initial installation.
Another frequent problem is inconsistent packaging speeds, typically brought on by mechanical wear or inadequate maintenance. Irregularity in rate can result in traffic jams, creating delays and lowering general performance. Furthermore, poor training of employees can exacerbate these problems, as operators might not fully understand maker capabilities or fixing techniques.
Furthermore, material jams are a typical event, frequently as a result of incorrect product specifications or international items blocking the machine's course. Such jams can stop production, requiring prompt treatment to clear the obstruction and resume operations.
Last but not least, digital faults, including software program glitches or sensing unit failings, can impede machine functionality - packaging machine repair service. These issues require timely attention, as they can cause prolonged downtime if not attended to quickly. Comprehending these usual problems is important for maintaining optimum performance and decreasing disturbances in product packaging procedures
Analysis Techniques for Repairs
Implementing effective analysis techniques is crucial for identifying and resolving problems in product packaging machines. A methodical technique to diagnostics allows technicians to pinpoint the origin reason of malfunctions effectively, consequently decreasing downtime and improving functional efficiency.
One of the primary techniques involves visual evaluations, where technicians analyze the machine for any evident indicators of imbalance, wear, or damages. This foundational action can typically reveal essential problems without the need for sophisticated tools. Making use of diagnostic software can significantly boost the troubleshooting process. These tools examine machine efficiency data, providing understandings into abnormalities that might not be right away visible.
One more crucial strategy is carrying out functional examinations. By methodically operating numerous parts of the device, technicians can observe efficiency disparities, helping to separate faulty parts. Furthermore, implementing vibration evaluation and thermal imaging can reveal covert troubles, such as overheating bearings or misaligned belts, which are usually precursors to much more significant failures.

Step-by-Step Repair Work Procedures
A comprehensive repair work procedure is important for restoring functionality to malfunctioning product packaging devices. The process starts with a detailed evaluation of the concern, making use of analysis methods to identify the origin of the malfunction. Once identified, collect the essential devices and replacement components to assist in the repair work.
Following, guarantee that the equipment is powered off and disconnected from its source of power to ensure safety throughout the repair service. Documenting the equipment's configuration prior to disassembly can assist in reassembly - packaging machine repair service. Very carefully remove any kind of panels or covers to access the malfunctioning components, noting any kind of particular screws or fasteners that need focus
Replace or fix the faulty parts according to the producer's requirements, making sure that all connections are safe. After reassembly, conduct a visual evaluation to validate that all parts web link are properly installed and that there are no loosened links.
When the maker is reassembled, reconnect the power and conduct tests to ensure proper functionality. Monitor the equipment during operation to determine any kind of residual problems. Record the repair work process, including parts changed and observations, to educate future maintenance initiatives. This meticulous method promotes ideal device efficiency and longevity.
Preventive Upkeep Practices
Preserving the functionality of product packaging devices is not exclusively reliant on reactive repair procedures; positive preventative maintenance methods play a substantial role in ensuring their long life and efficiency (packaging machine repair service). By carrying out a structured precautionary upkeep program, drivers can recognize prospective concerns prior to they rise into pricey breakdowns
Professionals must consistently examine parts such as belts, equipments, and sensing units for wear and tear. Furthermore, cleansing makers to get rid of dirt and particles is essential for optimal efficiency and to prevent contamination of products.
Training team on proper usage and handling of packaging devices can additionally decrease the risk of operational mistakes that might lead to tools failure. Establishing an upkeep schedule that includes regular checks and substitutes of important parts can dramatically extend the life expectancy of the machinery.
Documenting all upkeep activities not only aids in tracking the health and wellness of the devices yet also abides by regulatory standards. By prioritizing precautionary upkeep, business can guarantee their product packaging machines run at peak performance, eventually improving efficiency and minimizing downtime.
Tools and Resources for Technicians
Equipping specialists with the right tools and resources is essential for efficient packaging device repair work and maintenance. A well-stocked toolkit ought to include precision tools such as wrenches, calipers, and screwdrivers customized for specific equipment parts. In addition, diagnostic tools like multimeters and oscilloscopes allow specialists to determine electrical issues swiftly and properly.
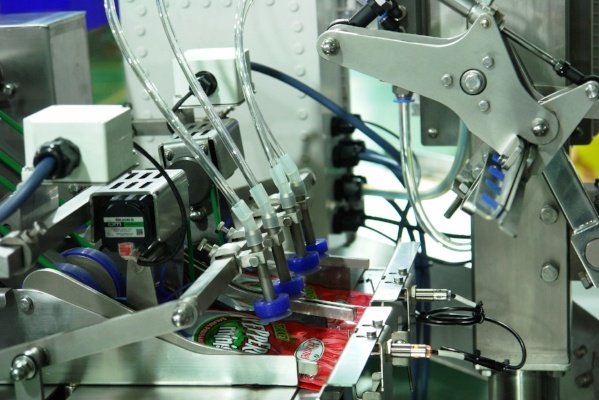
Moreover, purchasing software services for tools surveillance can enhance predictive maintenance methods. These applications assess machine efficiency data, notifying professionals to potential issues prior to they intensify.
Connecting with peers and signing up with market discussion forums can facilitate knowledge sharing and best practices among specialists, promoting a collective atmosphere for constant discovering. Keeping partnerships with vendors guarantees quick access to extra components and specialized tools, reducing downtime throughout fixings. By leveraging these devices and resources, technicians can boost their performance and efficiency in maintaining optimal efficiency of packaging machines.
Verdict
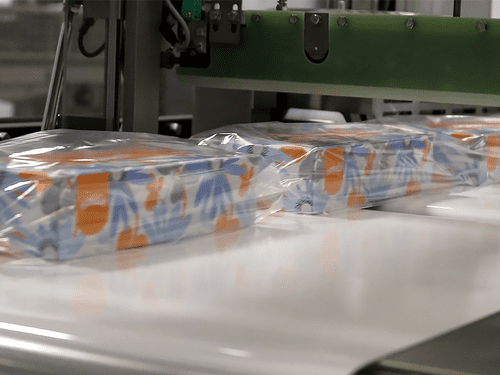
Efficient product packaging device fixing is critical for keeping operational connection and item top quality in today's hectic manufacturing atmosphere.Product packaging makers, vital for efficient manufacturing lines, frequently come across a number of usual problems that can interfere with operations.A comprehensive repair service procedure is necessary for restoring functionality to malfunctioning product packaging devices.Outfitting specialists with the right devices and resources is vital for efficient packaging maker repair work and maintenance.In final thought, effective product packaging machine repair service techniques are important for keeping optimal performance and lessening functional downtime.
Comments on “Trustworthy Packaging Machine Repair Service for Efficient Workflow”